Helical spring:
Helical springs are most commonly used in ” Suspension System”. They occupy smaller space and can have fixed or variable spring rates. Their energy storage capacity is higher than leaf springs. They are very light in construction and require no maintenance.
Or
A helical spring is a type of mechanical spring that is wound in the shape of a coil, typically made of steel or other elastic materials. It is designed to absorb and store energy when compressed, stretched, or twisted. The spring’s helical structure allows it to provide resistance and return to its original shape once the force is removed. This makes it a crucial component in various applications, including vehicle suspension systems, machinery, and household items like mattresses.
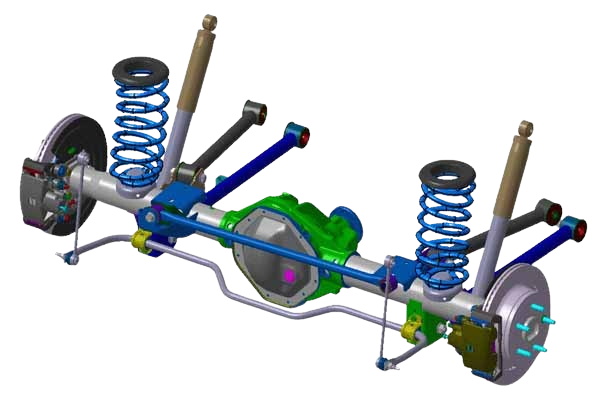
How Does a Helical Spring Work?
Helical springs operate on the principle of elasticity. When a force is applied to compress or extend the spring, it deforms but returns to its original shape when the force is removed. The spring’s ability to store and release energy makes it essential for absorbing shocks, maintaining tension, or providing support in a wide range of mechanical systems.
Advantages of helical coil spring:
-
Compact Design: Their spiral shape allows them to be more compact and efficient than other types of springs.
-
Versatility: Helical springs can be used in a variety of applications, from heavy-duty industrial machinery to everyday household products.
-
Durability: Made from strong materials, they are designed to last and maintain their functionality even under continuous stress.
Light in weight and requires smaller space. They take care of bending loads as well as vertical shear loads. Good vibration damping capacity and ability to absorb shocks.
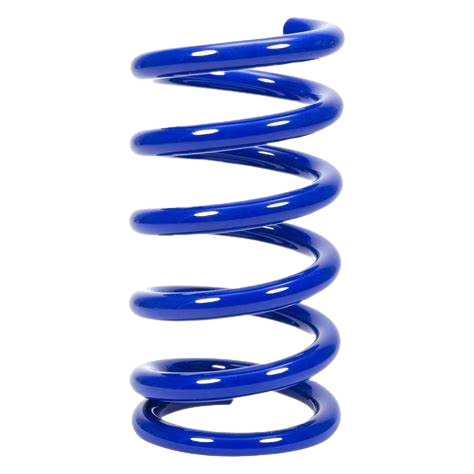
Disadvantages of helical coil spring:
-
- Lower load carrying capacity and hence cannot be u ed commercial vehicles like trucks.
- Difficult and costly to manufacture.
- Poor ability to take care of side thrusts and torque.
- Usually “Helper Spring”, i.e. additional spring (giving ‘nested’ construction) is needed.
Applications of helical coil spring:
-
- Used in all two-wheelers (like bikes, mopeds, scooter, etc.).
- Used in all three wheeled vehicles (like auto rickshaw, small pickup load carriers, etc.)
- Used in front suspension of LMV (light motor vehicles) like passenger cars.
1. Design Considerations:
When designing or selecting a helical spring for a specific application, several factors need to be considered to ensure it meets the required performance criteria:
-
Material Choice: The spring material affects its strength, durability, and fatigue resistance. Common materials include carbon steel, stainless steel, and alloy steels. For more demanding applications, materials like titanium or Inconel may be used.
-
Spring Rate: This refers to the stiffness of the spring, or how much force is needed to compress or extend the spring by a given distance. A higher spring rate means the spring is stiffer and harder to compress or extend.
-
Wire Diameter: The thickness of the wire used in making the spring influences the load-carrying capacity and durability of the spring. Thicker wires provide more strength.
-
Number of Coils: The number of coils determines the spring’s flexibility and load distribution. More coils generally provide greater flexibility, while fewer coils offer greater stiffness.
-
Free Length and Solid Length: The free length is the uncompressed or unstressed length of the spring, while the solid length refers to the length the spring will occupy when fully compressed. These factors must be designed to match the requirements of the specific application.
2. Helical Spring Manufacturing Process:
The process of making a helical spring typically involves several steps:
-
Wire Drawing: The raw material (usually wire) is drawn into the desired thickness using a drawing machine.
-
Coiling: The wire is then wound into a coil shape, using a machine that wraps it around a mandrel or die, forming the helical shape.
-
Heat Treatment: After coiling, the spring is heat-treated to improve its strength and elasticity. This process is essential to ensure the spring performs well under stress and retains its shape over time.
-
Grinding and Finishing: The ends of the spring are often ground to ensure flatness, and the spring may be coated or treated to resist corrosion or wear.
3. Helical Spring Fatigue:
One of the main challenges for helical springs is fatigue, which occurs when a spring is repeatedly stressed and deformed. Over time, the constant load on the spring can cause microscopic cracks that eventually lead to failure. To combat fatigue, high-quality helical springs are designed with specific materials and manufacturing techniques to enhance their durability. Regular maintenance and replacement of worn-out springs are essential in high-stress applications.
4. Helical Spring Testing:
To ensure the performance and reliability of helical springs, several tests are often conducted during the design and manufacturing process:
-
Load Testing: Springs are tested under various loads to determine their load-bearing capacity and how they respond to compression or tension.
-
Fatigue Testing: This test simulates the repeated loading and unloading of the spring to assess its fatigue resistance over time.
-
Dimensional Inspection: The spring is measured to ensure it meets the required dimensions, including wire diameter, number of coils, and overall size.
5. Helical Spring Innovations:
As industries evolve and technology advances, innovations are continuously made in the design and application of helical springs. These innovations include:
-
Variable Pitch Springs: Springs with coils that are spaced unevenly, providing a varying spring rate. These are used in specific applications where the load distribution changes dynamically.
-
Plastic Helical Springs: In addition to traditional metal, plastic materials like nylon are also being used to create helical springs. These plastic springs are lighter and resistant to corrosion, making them ideal for certain low-load or delicate applications.
6. Helical Spring vs Other Types of Springs:
Comparing helical springs to other types of springs can provide more context for their advantages:
-
Helical Springs vs. Leaf Springs: While leaf springs are best suited for heavy-duty applications, helical springs offer more compactness, greater flexibility, and smoother performance in vehicles.
-
Helical Springs vs. Coil Springs: The term “coil spring” is often used interchangeably with helical spring, but coil springs can also refer to other spring types (e.g., torsion coils). Helical springs specifically refer to a spring wound in a helix shape.
In conclusion, helical springs are an essential component in many systems due to their versatility and ability to absorb and store energy. Whether in vehicles, machinery, or household products, their simple yet effective design continues to make them indispensable in modern engineering.
Recent Comments